
Raising the Fuselage
Running Total Hours:
10.25
 | 2006.09.15:
(10.0) [this entry spans the
past two weeks] Since I brought home the fuselage from Van's I've had
it sitting on the garage floor. A furniture blanket under the
forward fuselage protected the bottom skin from getting scratched, and
some oversized pillows held up the tail. This arrangement worked
out very well for the past 16 months, giving easy access for working
in the cabin area and with no possibility of a disastrous fall.
But now it's finally time to raise the fuselage off the floor so I can
work on things like the landing gear mounts, cabin steps, and closing
out the tail cone. I decided to raise the fuselage about 19
inches off the floor, which will be a comfortable height to work with
my feet on the floor, and will give me sufficient ground clearance
underneath to work for the next few months, until I decide to mount
the gear legs. (Then I'll have to raise the fuse another few
inches, which I will do in a more temporary manner).
I decided to build two saw horses to support the fuselage: one under
the main bulkhead (where the wing spars attach) to support most of the
weight, and one under an aft bulkhead to support the tail. The
main support needed to be about 19" tall with a flat top sufrace
of 46" wide by 6" long (fore-aft). The tail support
needed to be about 30" tall with a conforming top that can
support the tail cone without damaging it.
Rather than build my own from scratch, I bought two steel saw horses
at Home Depot and modified them to my specifications. They were
already extremely strong, claiming to support over 1000 lb, but I
wasn't totally happy with their stability and rigidity to side
loads. So I added trusses made of 1/8" thick 1" leg
aluminum angle, attached using 1/4" steel bolts. This
easily stiffened up the horses to my satisfaction. Furthermore,
I cut the angles connecting the bottoms of the legs to each other
longer than the span of the legs, which effectively widened the
footprint of the horses making them more stable.
As for the top surfaces, I took two different approaches. For
them main horse, I bolted on a plank of 1"x6"x46" pine
and rounded over its edges using a router. I then cut a piece of
furniture blanket to upholster it like a chair. The furniture
blanket provides just a slight amount of cushioning to spread the
weight evenly, and should protect the bottom skin from scratches if
the fuselage shifts slightly. For the tail horse, I just took
some foam I had laying around and duct-taped it to the top beam of the
horse. The foam should be conforming enough to support the tail
without indenting it. |
 | 2006.09.17:
(0.25) With saw horses all
ready to go, I summoned my loyal laborers, eh, I mean friends, and we
had the fuse off the ground and onto the sawhorses in no time.
The operation went flawlessly. Thanks Jimmy, Vay, and John, for
doing the heavy lifting! And thanks Stacey, for coordinating the
operation and capturing this momentous occasion on film (or flash card
as the case may be)! It's funny how it's sometimes the small
steps that really provide motivation, and this is definitely one of
them. Up at roughly "on the gear" height, it suddenly
looks so much more like an airplane! |

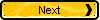
|
|