
Main Landing Gear
Running Total Hours:
0.0
 | 2007.02.09:
(25.0) [this entry is for
the past two weeks or so, time is approximate]
The main landing gear mounts are these massive steel weldments that
install on the forward side of the center section bulkhead. At
first glance, this task looked simple. Cut holes in the bottom
skin where the gear legs exit the fuselage, drop in the weldments,
bolt them to the existing holes in the bulkhead, and match-drill the
remaining bolt holes in the lower longerons. Well, this task so
far has been a nightmare of one problem after another. I must
say in this area I am not impressed with Van's design details or
manufacturing quality... All things that would have been easy to
fix by Van's in the kit, but are a PITA for the builder to fix at this
point. Instead of describing this mess as chronological prose,
I'll just go issue by issue.
The plans (DWG 34A) provide a template for elliptical holes that must
be cut in the bottom skin for the gear leg exits. I photocopied
the plans (making sure the scale is preserved), and used the
photocopies as stencils to mark the cuts, located in the fuselage
based on rivet locations. After cutting the holes per plans, I
found that I'd have to enlarge them by at least 1/8" all around
to fit the weldment. No surprise. But the problem is that
this places the aft edge of the hole half way through a rivet
connecting the center section bulkhead to the skin. I'm not
worried about giving up this one rivet, but I can't leave half a rivet
because that's inviting a crack to form. So I'll have to remove
even more material from the skin and center section flange to
eliminate the entire rivet. If only Van's left that rivet out in
the first place...
Had to remove the outboard three nut plates from the upper flanges of
the center section bulkhead. They interfere with maneuvering the
weldment into position. If only they had been left out...
Part of the weldment goes between the center section bulkhead and the
aft end of the outboard F-772B floor stiffeners. The stiffeners
as assembled per plans in the QB fuse do leave enough clearance for
the flange of the weldment, once it's in. But they don't leave
enough clearance to put it in or take it out. I had to trim the
vertical leg of the stiffener, angling its aft edge forward a little
to provide enough clearance to actually move the weldment into
position. This should not significantly affect the strength of
the stiffeners, and would have been very easy to do before they were
riveted to the fuselage. However, with the stiffeners already
riveted to the fuselage, it's a delicate and awkward operation with
potential for damaging the center section bulkhead (which would be a
major disaster). I covered the surrounding floors and center
section bulkhead with scrap aluminum and stainless steel, to protect
them from accidents while cutting. I then used the die grinder
with a cutting wheel, followed with some very careful filing. If
only the plans had the edge of the stiffeners cut at an angle...
Trying to bolt the weldment to the center section bulkhead, I
discovered that the "close tolerance" holes in the bulkhead
are actually quite misaligned. Although I was using standard
bolts for initial fitting (which have a slightly smaller diameter than
the close tolerance bolts), two of the holes (lower left) were so
misaligned that I couldn't even push a standard bolt through.
Upon closer inspection I discovered that the misalignment was
primarily between the F-704C and the rest of the bulkhead (see DWG
11). The main part of the bulkhead (the heavy bars and channel)
are drilled in assembly with the wing spars at the factory.
However, the vertical pieces F-704C and D are riveted onto the
bulkhead later by the builder, or in this case by the QuickBuild shop
in the Philippines. The builders manual clearly describes that a
couple of close tolerance bolts should be put in to keep things
perfectly aligned while riveting, which the QB shop evidently did not
do. Being that the wing attachment points are just about the
most critical structural component in the airplane, I decided to
consult Van's. The answer they gave me was not a surprise...
[paraphrasing]: "Yes, that's pretty common. File the F-704C
and D to remove the interference." If only the QB shop
followed directions... I'm not crazy about the idea of filing
the close tolerance holes, but I really don't see a better
option. I considered reaming through the holes, which would in
theory produce a cleaner, rounder hole. But even a perfectly
sized reamer is likely to enlarge the holes in the bars slightly,
which would not be good. Also, it would be difficult or
impossible to ream some of the holes simply because there's not enough
room to get a drill into position due to other structures in the
fuselage. So back to filing, which I think I can do without
affecting the bars. I decided to take a round needle file and
cover all of it in masking tape other than about a 1/2" length in
the middle. That way I can file the F-704C/D with the file
running all the way through the bars, but with the masking tape
protecting me from accidentally filing of scoring the bars. I'm
using a 0.239" pin (the shaft end of a 1/4" reamer bit) as a
feeler, checking for a "step" in the hole and filing
incrementally until there is no step. This is yielding very good
results so far, but is incredibly tedious and slow going. Today
I did 12 of the 32 holes, in just over 3 hours. After doing
this, I can insert a close tolerance bolt with reasonable finger
pressure.
So far the left weldment seems to fit ok, but the right weldment does
not. I finally figured out that the right weldment itself is the
problem. The flange at the end of the support tube that runs
toward the lower inboard part of the center section is out of plane
with the rest of the weldment. It sits approx 1/8" forward
relative to the rest of the weldment, and is at a bit of a funny
angle. It is such that even if I managed to bend the support
tube closer to position, the angle of the flange would only get
worse. I've decided that this is not workable, and I'm going to
ask Van's to exchange it. |
 | 2007.04.17:
(40.0) [This log
entry is for the past several weeks. Time logged is a gross
estimate. I've been very busy at my day job, so work on the
plane has slowed down considerably, but I have been working on it
little by little. Just haven't kept up in logging every work
session.]
After a few emails back and forth with Van's, they agreed to replace
my right gear weldment. The new one indeed was a much better
fit. Not perfect of course, but definitely workable. It
had a slight twist in the plane of the bulkhead, and the forward
support tube needed a 0.020" shim. As with the first two
weldments, the rivet clearance holes had to be opened up
considerably...
With both weldments basically fitted, I cut the exit holes for the
brake line fittings. Another minor nuisance here: There are
pilot holes pre-punched in the bottom skin where supposedly these
exits should be centered. The plans instruct to just enlarge
them to final size. In reality, they didn't end up being
perfectly centered with the holes in the weldments, which is what
really determines the position. So a little work with the Dremel
to nudge the hole over to clear the brake line fitting. |
 | 2009.05.01:
(0.0) Back to the
main gear as a background task, I decided to get the wheels, brake
calipers, and brake lines fitted to the gear legs. But first,
after a couple of years of sitting in the garage gathering dust and
gunk, the gear legs and mounts were in need of a serious
cleaning. Acetone always does just great, and it did, up until I
got the right main gear leg. The powder coat Van's applies to
all the steel parts is tough as nails and normally impervious to
acetone, but on the right main gear leg, that was not the case.
The powder coat on this particular part, and only on this particular
part, was rapidly desolved and ruined by the acetone. I couldn't
get any good answers as to why, but I suspect that the powder coat
must not have been applied or cured properly. Anyhow, the powder
coat needed to be removed (sand blasted off) and redone. I
talked to Ken Scott at Van's who said they would take care of it, but
suggested that I get it done locally to save on time and shipping
costs. I had it done at R.W. Little, a local shop recommended by
my neighbor Buzz. They charged me $50, and they had it done in
less than 24 hours after I dropped it off.
Back to forward progress... I fitted the brake flanges to the gear
legs. I also installed the fluid fittings on the brake
calipers. Each caliper has two NPT ports: the top one is used
for connecting to the pressure source (i.e. master cylinder side of
the system), and the bottom one is used for a bleed valve. The
bleed valves came already installed in the brake calipers, but on the
same port on both calipers. Since we need a left and a right, I
had to move the bleed valve to the opposite port on one of the
calipers. This was actually difficult to do without damaging the
bleed valves because they were installed with very high torque.
Anyway, mission accomplished, and I also installed the elbow fittings
in the other ports. I used Loctite 567 to seal the threads. |
 | 2010.09.02:
(0.0) Mounted the
tires on the wheels. Quick overview of the process: Split
the wheel by removing the three through bolts (CAUTION!: never do this
with a pressurized tire on the wheel!!!). Remove and discard the
nuts and washer from the valve stem of the inner tube. Apply
talc powder to the inner tube and the inside of the tire. Insert
tube into tire, valve stem pointing toward the red dot on the tire
sidewall (this is to help roll the airplane to valve-down
position). Inflate tube just enough for it to assume its shape,
so it won't get pinched between the wheel halves. Apply a touch
of grease to the end of the valve stem so it slides more easily
through the grommet in the wheel. Slide it through the grommet
in the wheel (this is the outer wheel half). Get the outer wheel
half and tire in the correct position relative to each other (the red
dot on the tire should line up with the valve stem). Set them
down with the outer wheel half down. Put on the inner wheel half
(with the brake disc) and slide in the three through bolts.
Press down a bit so it stays, and to make sure the tube isn't getting
pinched (feel/hear metal-to-metal contact). Stand the tire up so
both wheel halves are acessible. Install the nuts, first by
hand, then just taught with a wratchet (again double check that tube
isn't getting pinched), then to final torque. Note that
Cleveland doc that came with the wheel specified 90 in-lb, but a
sticker on the wheel itself specifies 75 in-lb, so I'll go with
that. These are AN4 bolts with what appear to be MS21042
all-metal stop nuts (presumably for high-temp from braking).
With the bolts properly torqued, it's time to inflate the tire.
It'll take some inflationg to seat the bead. Inspect to make
sure it looks good all the way around on both sides. Inflate
slowly to 25 psi. Deflate by removing the valve core, being
careful that it doesn't shoot out and take someone's eye out.
Reinstall the valve core and reinflate the tire to 25 psi.
Repeat this once or twice so that the inner tube can adjust itself to
seat properly with no kinks.

Note that the bearings may still need to be (re)packed before
use. To be revisited... |
 | 2010.09.18:
(0.0) Fit the
wheels to the axles. There are axle spacers that come from
Van's, as well as the axle nut. I elected however to buy a set
of modified axle nuts from Avery. Instead of having a closed end
cap, the ends are open, and a separate U-shaped bracket screws on to
close off the end (which holds a nut plate for mounging the wheel
pant). The purpose for the open end is to be able to jack up the
plane using a rod inserted through the axle nut into the hollow axle.
Back to work: The axle nuts are pre-drilled for cotter pins, but the
axle is not pre-drilled. I installed the axle nuts and used them
as drill guides to drill the axles. Not too tricky, and came out
well.
Note that there are many opinions out there on torquing axle
nuts. Van's instructions are simply to ensure that the wheel
turns freely and there is no side to side play. That's a start,
but it's also known that roller bearings tend to do better with some
pre-load. Reading through Cleveland's documentation, I found
some recommendations that are as follows: Torque the axle nut to
150 - 200 in-lb to seat everything into place. Then loosen it
back up, and re-tighten to 30-40 in-lb of torque. So that's what
I did. The final torque is at about 40 in-lb.
 |
 | 2011.07.18:
(0.0) In the
interest of getting it done, much work on the gear has gone
undocumented. But a quick summary:
I've permanently mounted the gear legs, using close tolerance bolts
sized for an interference fit.
I've discovered the there's some toe-in error in my gear. The
right main has zero toe (ideal), while the left main has about 1.3°
toe-in. Spoke with Van's about this, and they indicated that toe
may vary as much as +/- 2° in the tolerance specified for the bend in
the gear leg, and that this is both unfixable and not enough to be a
problem with ground handling or tire wear. Hopefully they're
right.
I completed fitting the gear fairings. I.e. all the geometry is
now fixed, and only the finish work (fill and sand, fill and sand)
remains.
Note that I ended up making my own intersection fairings after finding
quality and fit problems with the pre-fabbed intersection fairings
from Van's as well as two other vendors. Molding clay and doing
the layups was very very laborious, but the results made it worth
while.
With the gear fairings fitted, I took the fuselage of the saw horses
and rested it on the gear for the first time. This sets the
stage for mounting the engine.



First landing!
 |

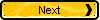
|
|