
Engine Selection
Running Total Hours:
0.0
 | 2009.01.14:
(0.0) Early in the
project I made some basic decisions about my choice of powerplant for
the airplane, which I will explain below. But in summary, I
decided to go with a non-certified clone of a Lycoming parallel-valve
IO-360, featuring an Aerosance (now part of Teledyne Continental
Motors) PowerLink FADEC in lieu of the traditional magnetos and
mechanical fuel injection. Mattituck, an engine shop that also
happens to be owned by Teledyne Continental Motors (TCM), has been
selling exactly such an engine to the experimental market: the TMX
IOF-360. Sadly, TCM, who bought out Aerosance some years ago,
has recently decided to no longer offer this FADEC system to the
experimental market, nor for Lycoming-style engines at all. TCM
cites lack of sufficient demand from the experimental market, and
their need to focus on the certified market. I doubt that this
is the whole truth (Lycoming recently announced their own FADEC in the
works), but in any case, TCM has made their
decision. TCM has also recently moved the FADEC group from
Aerosance's original home in Connecticut to TCM's home in Mobile,
Alabama. In the process, no surprise, they lost the key
people who developed the technology at Aerosance. So the whole
future of this product may now be in jeopardy. I have to say I
am very disappointed, but to some degree also relieved, at the timing. Had I
already purchased my engine, say a year ago, I would now be stuck with
an "orphan" product, and a dubious future for support and
spare parts.
So I'm back to the drawing board. I'm still planning to go with
a Lycoming clone parallel-valve IO-360, but I'm back to evaluating my
options for ignition and fuel metering.
Anyway, just for fun, I will document my engine selection process
here, including both past and present evaluations and decisions.
This is an interesting and hotly debated topic, and one that people
often ask me about (both pilots and non-pilots). So here it
goes, from the ground up.
AIRCRAFT ENGINES VS. AUTOMOBILE ENGINES
There have been quite a few people who have installed auto engines in
their aircraft. There are reasons why this seems enticing.
Firstly, auto engines are far less expensive than aircraft
engines. A new Lycoming engine costs more than a brand new
Subaru -- the whole car I mean, not just the engine. Secondly,
auto engines are generations ahead of aircraft engines in
technology. Because of regulatory and other obstacles in the
aviation industry, we're still flying engines that essentially haven't
changed in 50 years. While the auto industry on the other hand,
blessed with a free market business environment, intense competition, and high production volumes, has
moved forward in leaps and bounds. Auto engines are also
designed to burn auto gas, which is cheaper and has a less uncertain
future than leaded avgas.
But there is a dark side. The best auto engine in the world
still makes a poor aircraft engine. An engine in an
aircraft is subjected to operating requirements that are very
different from the operating requirements for an engine in an
automobile. Naturally, automobile engine designs are optimized
for their intended application: operating in an automobile. Many
of these design optimizations make them unsuitable for aircraft use.
1. Automobiles require short bursts of relatively high power output
for acceleration, and then only modest power output for steady state
cruising. It is very unusual for an auto engine (other than in a
race car) to operate anywhere near its "red line" RPM, or
anywhere near its max rated power output. Aircraft operations
normally consist of takeoff and climb at near "red line" RPM
and 100% power output, followed by steady state cruise at 80-90% of
red line RPM and 75% power.
Aircraft engines are designed to sustain that sort of operation
reliably over a 2000 hour service life. That same profile of
operation would be incredibly abusive to an auto engine, and would be
detrimental to its reliability and service life to an unknown degree.
2. Light aircraft engines are generally designed to spin a propeller
via direct drive, i.e. the prop is basically bolted to the crank
shaft. Now, propellers operate most efficiently, and produce
less noise, when the blade tips are well under the speed of
sound. The tip of a 72" diameter prop (typical for an RV)
traces an arc of approximately 18.85 feet per revolution. The
speed of sound at sea level, dry air, 20°C, is approximatel 1,125.79
feet per second. So the blade tip will be traveling at Mach 1
when rotating at 59.7 revolutions per second, or 3583.5 revolutions
per minute (RPM). Typical aircraft engines for this class of
airplane are designed to produce peak power outpout at a red-line 2700 RPM. Compared to auto engines, these
aircraft engines produce lots of torque at relatively low RPMs.
Auto engines, typically, produce very little torque at those RPM
settings, and are designed to produce their peak power at RPM settings
as high as 7000. This is well suited for automobiles, producing
smooth efficient operation when coupled with an appropriate
transmission and drivetrain. But in order to use such an engine to
spin a 72" prop, a reduction drive -- a transmission of sorts --
becomes necessary. This constitutes extra weight, extra friction
and heat, an extra critical failure point (and a highly significant
one as shown by the accident statistics), and extra cost that often
far exceeds the cost of the engine itself, thereby nullifying the cost
advantage over a traditional aircraft engine.
3. Aircraft engines are designed with certain measures for
mission-critical reliability, such as dual redundant ignition systems,
and independence from failure of the airframe's electrical
system. Auto engines, while generally very reliable, do not
posses this level of fault tolerance.
And more... Most auto engines are water-cooled, whereas most
aircraft engines are air-cooled. Water cooling is not
necessarily a killer,
but does present some practical challenges in aircraft: more weight,
more failure points, etc.
There are a number of vendors out there selling kits to convert
various auto engines for aircraft use. Some even specifically
for the RV. Some do a decent job under the circumstances.
But when all is said and done, they have no performance advantage over
traditional aircraft engines, no major operational advantages,
distinct operation disadvantages outlined above, and ultimately cost
at least as much when all the associated conversion and installation
costs are taken into account.
My bottom line: Shoe-horning an auto engine into
an airplane can be done, but ultimately is not a good fit. No
thanks.
OTHER ALTERNATIVES TO TRADITIONAL AIRCRAFT PISTON ENGINES
How about a diesel? Several companies have or are in the process
of developing and marketing diesel engines for light aircraft.
There are certain benefits to diesel, including the fact that they can
burn Jet-A or a variety of other suitable kerosene and bio diesel fuels, which will
likely remain available long after traditional avgas (i.e. 100LL) is
history. These diesel engines have seen some limited commercial success,
especially in Europe, in experimental as well as certificated
aircraft. However, they do have some major downsides. The
diesels are generally bigger and heavier for a given power rating
compared to traditional aircraft piston engines. As these are
new designs, there is still not a lot of history on any of these
engines, so their long term reliability remains to be seen. The
future of any specific engine and its manufacturer is also quite
uncertain, as we've seen with the recent collapse of Thielert, which
was one of the most promising players.
How about a turbine? Turbines have certainly proven their worth
in larger and higher-performance aircraft. Their power to weight ratio
is superb, as is their reliability and service life. However, they present some
practical limitations for my class of aircraft. They are not
very available, not well supported, and still too expensive to put in
a little RV. Their fuel efficiency is also abysmal compared to
piston engines, making the aircraft's operating costs (predominantly
fuel costs) much higher.
How about electric? I wish! An electric powered airplane
could be far more reliable, more energy efficient, and far less noisy
than piston power. This IS coming, but it's not here quite yet.
There are a few concept prototypes of electric airplanes out there,
but they are basically underpowered motorgliders with very limited
performance, range, and endurance. The biggest obstacle right
now is lack of a battery technology that has sufficient energy density
to even come close to that of petroleum-based fuels. I'm sure we will have
this some day, maybe even within the next few years. But the
technology will
likely be driven by the auto industry as it pushes toward electric cars, and
then we can adopt the technology for aircraft use.
TRADITIONAL AIRCRAFT ENGINES: LYCOSAURUS REX
They are certainly outdated in comparison to the state of the art of
piston engines outside of aviation, but the venerable Lycoming engines are still the
industry standard for this class of light aircraft. These are
available in various displacements and configurations, but for the RV
series basically all are horizontally opposed, normally aspirated, air
cooled engines that will spin a propeller in direct drive.
In their stock configuration, they employ dual magnetos for redundant,
electrically independent ignition, and either a carburetor or
mechanical fuel injection servo for electrically independent fuel
metering. The throttle control in the cockpit directly controls
an intake air butterfly valve, and a mixture control in the cockpit is
used to adjust the mixture for atmospheric and operating conditions
throughout the flight. Optionally, these engines also have
provisions for a hydraulic constant speed prop, also via a dedicated
control in the cockpit.
These engines, if treated right, are fairly reliable, and have a TBO
of approximately 2000 hours. However, their primitive design
does require a fair amount of knowledge and attention from the pilot
to keep the engine happy. This is not a "turn the key and
go" engine like we've become accustomed to in our cars.
These engines are also not cheap. A certified Lycoming IO-360
for example can cost in the neighborhood of $30K to $40K new.
Update 2009.04.17: One of the issues currently facing these engines is
that they were designed to burn high-octane leaded gasoline.
Their favorite blend, 100LL avgas, has been widely available for
decades, but may disappear within the next few years due
to increasing economic and environmental/regulatory pressures to
eliminate the use of lead additives. Tests have shown that most
of these engines (except for high compression and turbo-charged
variants) can operate just fine using various high-octane unleaded
fuels. But contemporary auto gas is not an option due to the now
mandatory inclusion of some fraction of ethanol in the blend (thanks
to the corn growers' lobby masquerading as environmentalists...
argh!). Ethanol is a poor automotive fuel, and even more problematic for
aviation use for several reasons, but that's a whole other
discussion. Anyway, currently there are several different fuels
being proposed as replacements for 100LL avgas, but it remains to be
seen which will emerge victorious, how available it will be, and how
much it will cost. The best bet for now is to try to make
choices that will support the broadest spectrum of possible fuels in
the future.
TRADITIONAL WITH A TWIST: LYCOSAURUS CLONE
In the experimental category we are not required to use certified
engines, and so most opt for a slightly cheaper and less restrictive
alternative. There are several engine shops out there that build
"experimental" Lycoming-clone engines, meaning ones that
have not been blessed by the FAA. In most cases, these engines
are built from all or most of the same FAA-certified parts. In
some cases these engines are totally identical other than a piece of
paper and/or data plate. In other cases, modifications are made to the builder's
needs, or to alleviate known deficiencies in the certified engine that
have not been remedied
due to the excessive regulatory burdens associated with design changes to
FAA-certified equipment.
Among the more common modifications in these Lyco-clones are
improvements in lubrication, alternative cam profiles, roller tappets,
and electronic ignition. And yes, a somewhat lower price (but
not much lower...).
For me, the Lycoming clone option represents the best compromise among
what's currently available, so that's what it'll be.
ENGINE CLASSES AND VARIANTS
Van's designed the RV-7A to accept a range of Lycoming-style engines
with displacement between 320 and 360 cubic inches, and between 160
and 200 horsepower. This effectively translates to one of three
major engine classes: the 160 HP parallel valve (I)O-320, 180 HP
parallel valve (I)O-360, and 200 HP angle valve (I)O-360. The
parallel valve 320 and 360 are very similar in design, size, weight,
and cost, with the 360 just being a little bit bigger and more
powerful. The angle valve 360 is a distinctly different design
from its parallel valve cousins. The angle valve 360 puts out 20
horsepower more than the parallel valve 360, but is somewhat larger,
significantly heavier, and significantly more expensive. Van's
website shows performance data with each of these three engine classes.
This data is reasonably accurate according to other builders who have
completed and flown their RV's.
For my airplane, I have decided on the 180 HP parallel valve
IO-360. This represents a good compromise between performance,
range, fuel economy, weight, and cost.
IGNITION AND FUEL METERING TECHNOLOGIES
Back to the topic that sparked this write up. Traditionally,
these engines have used dual magnetos for ignition, and either a
carburetor or mechanical fuel injection for fuel metering. The
biggest advantage of these devices is that they do not depend on the
aircraft's electrical system to operate. Historically, aircraft electrical systems were known to be highly
unreliable (same technology as automotive electrical systems of the
1950's), and so making the engine's ignition and fuel metering
independent of the electrical system was vital. Mags and
mechanical fuel metering fit this requirement. But the disadvantages of these
ancient devices, however, are
many. Firstly, they are themselves fairly unreliable by modern
standards, being finicky mechanical contraptions with moving parts
that regularly wear out or go out of adjustment. Secondly, even
at their best, these devices perform their jobs in a fairly crude
manner, lacking sufficient accuracy or intelligence to operate the
engine at its best. As a result, engines using these devices can
be difficult to start, run rough at some power settings, produce less
peak power than they otherwise could, and burn more fuel than optimum
at all power settings. Thirdly, most of these setups include a
manual mixture adjustment that the pilot must manipulate during
different phases of flight to adjust for altitude and other operating
conditions.
At the opposite end of the spectrum is an alternative known as FADEC
(Full Authority Digital Engine Control). This technology uses
computer technology to continuously adjust fuel injection and ignition timing
based on the engine's current operating parameters as measured through
an array of sensors. A FADEC engine effectively monitors and
manages itself, far better than a human ever could, and the pilot is
mostly out of the loop other than selecting the power setting with the
throttle. Better-running engines and reduced pilot workload -- I
love it! We have taken this for granted in our automobiles for
some time, but general aviation has been slow to adopt this
technology. There are many reasons why, but most are not
technical. Rather, many are simply paradigm paralysis or
resistance to change in one form or another, both institutional and
individual. Anyhow, the biggest
technical implication for an aircraft builder installing a FADEC
system is that it does make the engine electrically dependent.
That means that sufficient safeguards must be designed into the
aircraft's electrical system such that the probability of total
electrical failure which leads to loss of engine power becomes
negligible. This is not difficult to accomplish, but does
require a level of electrical system redundancy that traditionally
hasn't existed in single-engine GA aircraft. There are well
known electrical system architectures that meet these needs and have
been in use on twin engine aircraft for some time. It is now
time to bring them to the singles. Incidentally, the GA market
is now finally moving toward glass cockpit technology in lieu of
traditional flight instruments, which brings forth the same
requirements for electrical system reliability. So FADEC and
glass cockpit technology naturally go well together. Good
riddence to the magneto, mechanical fuel servo, and vacuum pump!
There are also a variety of products out there that are not quite full
FADECs, but somewhere
inbetween, mostly in the form of stand-alone electronic ignition
systems. Electronic fuel injection systems are still not nearly
as common.
Following is a review of several products currently on (or off) the market.
AEROSANCE/TCM POWERLINK FADEC
The Aerosance
PowerLink FADEC was my solution of choice until Teledyne
Continental Motors pulled it from the experimental market. This
appears to be a well designed system, is field proven in over 100
installations and many thousands of flight hours over several years,
and for what it's worth (not much) it's even FAA certified on certain
engines. The system is fairly sophisticated, implementing
variable ignition timing and closed-loop pulsed fuel
injection, individually per-cylinder. People flying with this
system report smooth, reliable, fuel-efficient operation. I'm
sorry to see it go.
Update 2009.08.27: Continental's presence at Oshkosh 2009 was
conspicuously meager. They had their usual large tent, but it
was mostly empty space. That's curious, and a bit
disconcerting. Anyhow, speaking briefly with a couple of the TCM
representatives, they made it quite clear that they have no intention
of making the FADEC available again for the experimental market any
time in the foreseeable future. Not surprising, but
confirmation.
LYCOMING iE2 INTEGRATED ELECTRONIC ENGINE
Lycoming
announced in 2008 that they're working on their own FADEC system named
iE2
("Integrated Electronic Engine"). The system's
capabilities, from the info released thus far, will be even more
comprehensive than the Aerosance product, including its own electrical
power generation, knock detection, prop control, and turbo
control. But unlike the Aerosance product, the iE2 will not be a
bolt-on solution, but rather an integral component of Lycoming's new
engine designs. In other words, it will not be retrofittable to
legacy engines. Lycoming is initially targeting the iE2
technology at a 350 HP turbo-charged TEO-540-A engine for the piston
version of the Lancair Evolution, and a 116 HP IO-233-LSA engine for
the light sport market. No word yet on when/if Lycoming may
produce an iE2 version of an IO-360 class engine, which would be
suitable for use in an RV-7. I will be watching the iE2 system
with great interest, but I'm going on the assumption that it will not
be there in time for me to use on my airplane. I suspect that it
will also be VERY expensive, at least initially.
Update 2009.08.27: Lycoming's overall presence at Oshkosh 2009 was far
more dominant and impressive than Continental's. Also, Lycoming
seems much more interested in getting a piece of the experimental
(i.e. non-certified engine) market. I attended a technical
presentation on their IE2 system, which was very informative and
interesting. The system is quite sophisticated and capable, well
beyond even the Aerosance system. It looks promising
technically. But unfortunately for me, application of this
system to the 360-class engine is still likely years away, and even
then it won't likely be made available for customers like
myself. The Lycoming folks insist that the system doesn't just
need to be adapted to the engine type, but also needs to be integrated
and tuned with the specific airframe. Their intention is to
accomplish this by working with the airframe OEMs, developing standard
installations for the aircraft types, which can then be made available
as complete packages to customers through the airframe OEM's (the
Lancair Evolution is the first example of this). So in theory
the same could be done with Van's, and in fact one might think that
with the size of Van's market this would be a high priority for
Lycoming. But it doesn't appear to be. And furthermore,
given the penny-wisdom and resistence to new technology that's
prevalent at Van's and a good portion of the RV community, I suspect
that there won't be much "pull" for that either. So I
won't hold my breath.
PRECISION AIRMOTIVE EAGLE EMS
I first learned of the Precision
Airmotive Eagle EMS (Engine Management System) at a presentation
held at Oshkosh Airventure 2007, while the system was still under
development. Like the Aerosance product, the Eagle EMS
impelements computer-controlled electronic fuel injection and
ignition, although it is more rudimentary in its operation than the
Aerosance product. The Eagle EMS uses fixed ignition timing just
like a magneto, and controls the mixture in open loop. The
system hasn't yet gotten much test time in the field as far as I know,
but I look forward to pireps when it has. It is currently priced
somewhere between (formerly) the Aerosance product and a traditional
setup. If it proves to be a solid reliable product, it may very
well be the best offering available to the RV market, now that
Aerosance is out. I'll be watching the Eagle EMS with
interest.
Update 2009.01.27: I've learned some more about the Eagle EMS, and
it's a mixed bag.
The good: There are currently 14 of these in the field, at
least 2 of which are flying in RV's. These systems are now
available through Aerosport, a highly reputed engine shop. And
the Eagle EMS has been receiving increasing levels of attention in the
RV community, so hopefully this will help break "the FADEC
barrier".
The bad: There are some technical aspects of the Eagle EMS that
I really don't like.
1. They are now shipping with a manual mixture adjustment knob (a
potentiometer in the cockpit wired to the ECU) and have the pilot
tweak it for different phases of flight. That seems to defeat
one of the main advantages of EFI. I interpret that to mean that this
system just doesn't do as well as it should without pilot
intervention. If that's the case, that's a deal breaker for me.
2. The physical architecture of the system includes too many
"boxes", some of which are rather large, which makes for a
cumbersome installation. On the forward side of the firewall
there is a very big ECU box, two boxes containing the coils, a power
management box, and a dedicated battery (more on this later).
That's just a lot of "stuff" on the firewall, taking up
space, adding weight, and requiring a vulnerable wiring harness to
connect it all up. I would much prefer a system that would fit
within the physical confines of what it replaces, i.e. just bolt on to
the magneto pads (E-Mag did this nicely!) and intake. The number
of separate "boxes" should be kept to a minimum, and
especially any extra "boxes" on the firewall should be kept
to a minimum.
3. The Eagle EMS was originally designed to drop in to a traditional
certified airframe (Cessna 172) with only a single electrical system,
so a dedicated backup battery was designed in as an integral part of
the Eagle EMS. This makes it a poor fit for an airframe like
mine, which will already have dual indpendent electrical systems in
order to support an all-glass cockpit.
4. Precision Airmotive apparently is not developing or testing the
ignition and fuel injection maps to be used on any particular class of
engines. Rather, they leave it up to the engine shop and/or the
aircraft owner to "calibrate" the maps for that particular
engine (not just that type of engine, but each individual engine!). So even if the system hardware
and software were well designed and
tested, the maps may not be. That may also be a factor in
Precision's inclusion of a cockpit mixture adjustment knob, if they're
expecting that people will be running with poorly calibrated mixture
maps.
Update 2009.08.27: Attended a technical presentation at Oshkosh 2009
on the Eagle EMS. No news and no new details that I didn't
already know. The only new development that they're working on
is adapting the system to a six-cylinder engine. Still sending
mixed messages about the necessity the manual mixture adjustment knob.
LIGHT SPEED ENGINEERING PLASMA CD IGNITION
The Plasma II Plus and
Plasma III Capacitor Discharge Ignition systems from Light Speed
Engineering are standalone electronic ignition products that
implement high spark energy and variable ignition timing to provide
increased engine performance in comparison to a magneto. This
product line has been around for many years, and is available through
most of the major experimental engine shops. Pilots who use it
report that it indeed delivers the performance it promises, and many
are very happy with it. However, there have also been a
significant number of reports of failures associated with heat or
vibration damage. From others' descriptions (I haven't had the
chance to see for myself), it sounds like the component selection and
industrial design of these units is just not up to par. For
example, it uses DB-9 connectors and household wiring in the engine
compartment to connect to the hall-effect crank position sensors on
the magneto pads, which has been the source of many reported
problems. Also, the method of mounting the circuit board inside the
main box allows the board to vibrate within the enclosure and damage
the connectors and other through-hole components. If these
descriptions are accurate, then I'll have to write this product off as
too much of a tinkerer's radio shack project and not a robust
design. Bummer.
Update 2009.08.27: Stopped by their booth at Oshkosh. No new
development taking place. Just selling more of the same.
E-MAG
A relative newcomer, E-Mag is
another standalone electronic ignition product that takes advantage of
a strong spark and variable ignition timing to improve engine
operation. The E-Mag concept
has some distinct advantages over the Light Speed product though, most
notably in form factor. The E-Mag is completely self-contained
in an environmentally-sealed enclosure that sits right on the magneto
pad of the engine, whereas the Light Speed product has several
components spread across both sides of the firewall and connected with
cables of dubious quality. E-Mag also has a model known as the
P-Mag that
incorporates a small built-in alternator giving it an independent power
source, while it can still also run from ship's power as a backup.
There were some problems reported with early versions, but it sounds
like the company has been responsive in incorporating design changes
to correct the problems. I haven't closely followed the field reports on E-Mag
lately, so it remains to be seen if it ultimately proves
reliable in the field. I hope so. E-Mag is also planning
to certify their product, with all the good and the bad that that
entails.
Update 2009.08.27: Visited their booth at Oshkosh 2009. A
certified variant is now going into Lycoming's new IO-233-LSA
engine. It has a different form factor, puts two channels into
the same box, uses more rugged environmentally-sealed connectors, and
uses discrete logic instead of a microcontroller (to alleviate
certification requirements). On the non-certified side, the
114-series P-Mags seem to be past their growing pains and are
accumulating significant flight time in customer aircraft (including
many RV's). Studying the unit up close, I'm again a bit
disappointed with the choice of connectors. They are screw
terminal type connectors that are not environmentally sealed and have
no provision for strain relief (what's with these electronic ignition
guys and their choice of connectors???). [Update, Oshkosh 2010:
There is now a provision for a cushioned clamp on the chassis for
strain relief of the wire harness.] They reassured me that
the electornics are potted to prevent moisture intrusion, and that
they've never had problems with the connectors, although they admitted
that other customers have expressed the same concerns. So why
not just fix it? I'd be happy to pay a few more bucks for the
good connectors they used on the certified unit.
SIMPLE DIGITAL SYSTEMS EM-4
Simple
Digital Systems makes electronic fuel injection systems for a
variety of engines, both aircraft and automotive. I don't know
much about this product line yet. As far as I know, all their
installations use the same core hardware, which is highly field-proven
in cars but less so in aircraft. And of their aircraft
installations, most are auto conversions or other
"alternative" engines. They have had the system set up
on a Lycoming, but it sounds like this presents a more difficult case
for them, and has not been a popular choice (and therefore has not
benefitted from much refinement or test time). Unofficial rumors
are that one of SDS's customers has developed a kit for installing the
system on a Lycoming and is now starting to test it. We'll keep
an eye out for that. |
 | 2010.08.05:
(0.0) My mission
at Oshkosh this year was to finalize my engine choice down to the
details and select the engine shop. It took many hours of
discussion with the various vendors over a span of 3 days, but I was
able to get all my questions answered to my satisfaction, and arrive
at a clear winner. The following week I placed the order.
Note that I placed the order now in order to take advantage of the
good deals offered at the show, but I'm scheduling delivery for later
in the year, around mid-November when I expect to be ready for the
engine. I'll summarize
the details of the engine below:
Engine shop: Aero Sport Power
Aero Sport
Power (Kamloops, B.C., Canada) is an engine shop that
specializes in the experimental market, and has earned a solid
reputation among their customers in the RV community. Engine
guru Bart LaLonde and sales manager Sue Gregor were both at the event,
and I had the pleasure of speaking with them at length. Both are
very knowledgable and helpful. In
choosing their shop it came down to having the right offerings at the
right price, having the willingness to work with me to meet my
specific requirements, and that I can see that they take pride in their work,
will stand behind their product, and provide good support when needed.
Note that the first runner up was Teledyne
Mattituck (Mattituck, NY), which is also a highly reputed engine
shop with similar offerings and competitive prices. I think
Mattituck would also have been a fine choice, but a few
details ultimately gave the edge to Aero Sport.
Base engine configuration: IO-360-B1B
Fundamentally this is a non-certified clone of the certified Lycoming
parallel valve IO-360. The parallel valve IO-360 is a long-time
work horse in the general aviation fleet, and is a good reliable
engine. This particular variant is configured for constant speed
prop, vertical ("updraft") induction, a compression
ratio of 8.5:1, and is nominally rated at 180 HP.
Flat tappets
There has been much talk over the past couple of years about roller
tappets. Although commonplace in auto engines, roller tappets
were first introduced into aircraft engines a few years ago by the now
defunct Superior Air Parts, and later by Lycoming. The roller
tappets are meant to alleviate cam lobe spalling problems that
historically have affected these engines. Sounds like a good
idea, but comes at a hefty premium (>$2k). Most of the engine
shops now offer both the traditional flat tappets, as well as the new
roller tappets as an option. But the feedback I had gotten from
all of them without exception was that the roller tappets really only
add benefit to engines that sit for long periods of time (months)
without flying, therefore being much more prone to accumulation of corrosion.
Otherwise, there is no performance gain associated with roller
tappets, and flat tappet engines that are flown regularly don't tend
to experience any significant cam lobe corrosiong and spalling. So I decided to
stick with the flat tappets and save some money.
ECi Titan nickel carbide cylinders
The Titan nickel carbide cylinders from ECi
have better corrosion resistance, faster break-in, and lower cost than
Lycoming's nitride cylinders.
Note that some ECi cylinders
were affected by mandatory service bulletins and ADs issued in 2008 and 2009 for
a problem with potential cracking at
the cylinder head to barrel interface. The issue has since been resolved, and cylinders
now being produce and installed on new engines are not affected by
this issue.
Other major engine components: ECi
The engine shops tend to build the entire engine from either ECi
or Lycoming parts (although this is not strictly a requirement, since
they are interchangeable). ECi components are generally a bit
less expensive than Lycoming, and by all accounts just as good in
quality, so that's what it'll be.
Fuel injection: Precision Airmotive Silver Hawk EX
The certified ancestors of this engine use the venerable Bendix
RSA-5AD1 fuel injection system. This system is currently
produced by Percision
Airmotive, and continues to be used on certified Lycomings. Precision
Airmotive also produces the Silver Hawk EX, which is a
non-certified clone of the RSA-5AD1. Physically, the Silver Hawk
differs from the certified RSA-5 in its method of manufacturing.
The main housing of the certified RSA-5AD1 servo is cast aluminum,
whereas the non-certified Silver Hawk's servo (known as model EX-5AV1)
is machined from aluminum billet. According to Precision, modern
CNC technology makes the latter no more expensive than the former, and
eliminates the RSA-5's problems with casting porosity. There is
also another superficial difference in that the certified RSA-5 is
black anodized, where as the Silver Hawk EX is clear anodized (hence
the silver appearence). And that's about it. Otherwise
they are identical in operation, and their parts are interchangeable.
The variant of the Silver Hawk EX that I am getting actually has one
more difference. In the standard variant of the Silver Hawk (as
well as the RSA-5), the mixture lever is oriented downwards and swings
below the bottom of the servo, which is known to interfere with Van's
standard airbox. A common solution that is now available as an
option from Precision is an "alternate rotation mixture"
variant, where the mixture lever is oriented up instead of down, and
rotates in the oppositve direction so that it is still rich-forward /
lean-aft without having to use a bellcrank or other mechanical
contraption to reverse the direction of the control cable.
Reportedly, with this option, Van's standard airbox can be used
without modification, as well as Van's carburator mixture
bracket. The alternate rotation mixture variant for my engine is
kit # EX360-3 (whereas the standard kit is # EX360-1). The
physical differences are limited to a couple of internal parts, and
the servo could be converted back and forth if needed (by Precision, not in the
field). So the part numbers are as follows:
Kit # EX360-3:
1ea Servo p/n 3015010-1 (model EX-5AV1 with alternate rotation
mixture)
1ea Flow Divider p/n 3015004-1
4ea Nozzle p/n 2524864-2
Regardless of the mixture rotation option, the fuel inlet fitting can
go either on the left next to the mixture lever (typical) or on the
right next to the throttle lever. The fuel outlet fitting of the
engine-driven fuel pump is on the left side, so it probably makes for
more direct routing of the fule hose to have the fuel inlet fitting of
the FI servo on the left side as well.
This fuel injection system is relatively low-maintenance. The
only scheduled maintenance items are to clean out the inlet finger
screen and replace three o-rings in the inlet cavity at each
annual. The only other field-adjustable item is the idle
mixture. And otherwise it is expected to be maintenance-free
until overhaul, which is specified at the engine's overhal (2000 hour
TBO) or 10 years, whichever occurs first.
All "rubber" components (o-rings and diaphragms) are now
made of fluorosilicone, which is compatible with all known fuels,
including ethanol. A good thing as a contingency, looking
pessimistically into the future of aviation fuel availability.
Note that I had also considered some newer fuel injection systems from
Airflow Performance. These are still continuous-flow
all-mechanical systems, but claim higher performance than the older
RSA-5 style systems. By all accounts the Airflow Performance
FI's are good systems. However, the performance gains are minor,
the installations more complex, they are more expensive, have less of
a service history, have single-source parts, and are unfamiliar to
most A&P's in the field so they can only be service by Airflow
Performance. For those reasons I decided to stick with the RSA-5
based Silver Hawk.
In the past I had also considered the Aerosance FADEC and other
electronic fuel injection solutions. I still believe that EFI is
a better solution in principle, and I hope that solid viable products
will emerge in this space in the future. But to face facts, I
have to say the the EFI products currently availble for this class of engine are just not quite there yet. So,
sadly, the prospect of EFI will
have to wait, perhaps until my first engine overhaul.
Ignition: Dual P-Mags
The P-Mag (form company E-Mag)
is a self-contained electronic ignition system that fits into the form
factor of a traditional magneto. These deliver a stronger spark
than magnetos, support variable timing advance as a function of MAP
and RPM, and should enjoy a long maintenance-free service life with no
mechanical wear (no "points"). This product has had
its growing pains when it first arrived on the market, but has since
proven itself to be reliable and robust in the field over the past
couple of years (even Lycoming is now OEMing it on their new light
sport engines). The P-Mags, as opposed to the original E-Mags,
are also self-powering above idle RPM via a small internal
alternator. Ship's power is only used for start-up, at very low
RPMs (lower than flight idle), and as a backup in case the P-Mag's
internal alternator fails. In my case, I will have dual
electrical systems anyhow, and so each P-Mag will receive its ship's
power from a different electrical system for added redundancy.
Automotive spark plugs, aviation bosses, adapters
The P-Mags support either traditional aircraft spark plugs or
automotive spark plugs. The consensus seems to be that
automotive spark plugs are the best choice all around. Having
been designed with modern automobiles in mind, they are
designed to support a stronger spark, and therefore don't erode as
quickly as aviation plugs when using electronic ignition.
Automotive plugs are also available in more heat ranges. And as
an added bonus, as anything
automotive vs. aviation, the automotive plugs are far less
expensive. To their credit, aviation plugs are RF-shielded, whereas auto plugs
are not. But with modern resistive plugs and modern avionics
(anything newer than ADF...) this doesn't present any problem with RF interference.
Aviation plugs have 18mm threads, whereas auto plugs have 14mm
threads. As an available option, the bosses on the cylinders can be threaded for
14mm so that automotive plugs could be used directly. But although I plan to use auto plugs, I
opted for
the bosses to be threaded for the standard 18mm aviation plugs, and I will then
use 18mm-to-14mm adapters along with the auto plugs. That gives
me the flexibility to use either automotive or aviation plugs in the future without having to
re-machine the bosses.
Starter: Sky-Tec 149-NL
Sky-Tec model
149-NL "High-Torque Inline" starter is reputed to be strong,
durable, and reliable, and is a popular choice on these engines.
It also has a unique feature called the "Kickback Protection
System", which is essentially a field-replaceable sacrificial
shear pin that is meant to fail before damage could be done to the
engine's ring gear in case of kickback.
The other common choice is Sky-Tec model 149-12LS
"Flyweight" starter, which is both a pound lighter and a bit
less expensive. But this model is
reputed to suffer from occasional problems with cracking and
deformation of its housing, which can also lead to damage of the
engine's ring gear by engaging it off-axis. So in this case I
decided to go with the more reliable solution at the expense of an
extra pound of weight and a few bucks, and chose the NL.
Straight spin-on oil filter adapter
Several styles of spin-on oil filter adapters are available for these
engines, including straight and right angle variants. While the
right angle adapters look like they may make it easier to remove the
filter, I've been advised that the straight adapters actually make the
job easier and less messy. Just slip a "bread bag"
over the filter when you remove it, and the bag will capture any oil
that may drip out. According to Bart, the right angle adapters
are the only choice for Cubs due to the limited space between the
engine and firewall, but RV's have ample space and so a straight
adapter is possible and preferred. So a straight adapter it is.
|
 | 2010.11.02:
(0.0) The engine
shipped from Aerosport!
|
 | 2010.11.04:
(0.0) The engine
cleared customs (entering the U.S. from Canada). |
 | 2010.11.10:
(0.0) The
engine arrives. What a beautiful beast!
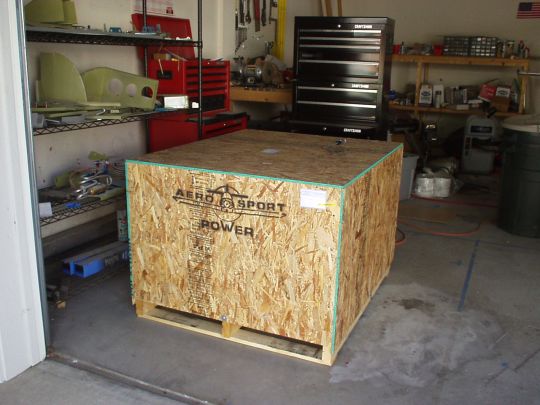


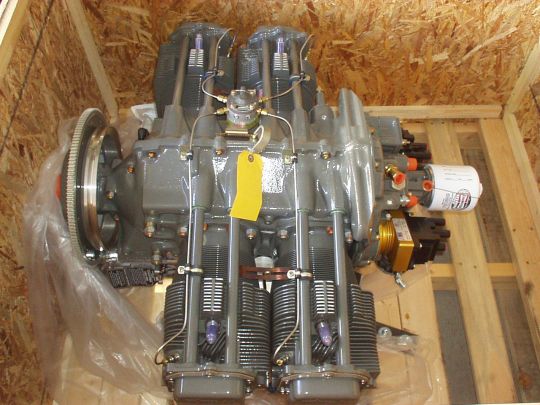 |

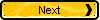
|
|