
Auxiliary DC Power Distribution
Running Total Hours:
0.0
 | 2011.03.07: (0.0)
The auxiliary electrical system is a low capacity but fully functional
electrical system independent of the main electrical system. The
broader aspects of the airplane's dual electrical system architecture
and its operational and reliability attributes will be discussed
elsewhere (where?). Discussions on this page will be limited in
scope to the power distribution components of the auxiliary electrical
system.
Aux alternator
The auxiliary alternator is a B&C SD-8 permanent magnet
alternator, a.k.a. dynamo. This simple device is driven by the
AND20000 vacuum pump pad on the engine's accessory case and weighs
only 3 lbs. It has a wound stator and permanent magnet rotor, so
there is no field winding, and no slip rings. It produces
2-phase AC output, unconditionally, any time the engine is
turning. A rectifier / regulator module and a few other support
components are required in order to harness it for well-behaved DC
current. It'll produce up to about 8 A at 14 V at cruise RPMs,
far less at low RPMs.
Mounting the SD-8 to the engine...
The vacuum pad gasket is Lycoming p/n 8313, Superior p/n SL8313, ECI
p/n AE9134, Teledyne Continental Motors p/n 653487 (what came with the
SD-8), or generically AN4045-1 or MS9134-01.
The pad has four 1/4 inch studs to secure the vacuum pump, or SD-8 as
the case may be. Hardware stackup is standard AN960-416 flat
washer, MS35333-40 internal tooth lock washer, and hex nut. Per
Lycoming document SSP1776, torque on a 1/4 inch nut 96 in-lb.
Three of the four nuts are readily accessible, but the fourth (lower
left) is practically impossible without specialty tools (or by
removing the right mag, highly undesirable). Both Rapco and
Tempest (vacuum pump manufacturers) offer purpose made wenches that
are offset to reach around the vacuum pump and get to that nut.
But these are only hand wrenches, no provision for a torque wrench, so
it solves only half the problem. In talking with people I've
found that just using the "gutentight" method on that one is
common. Ok... But I found another tool, sold online here,
that gets it right (mostly). Instead of a handle, this one
provides a 1/4" drive receptacle, so it can be used with a simple
handle, ratchet, or torque wrench. $35 -- sold. Now one
thing that's still not ideal about this tool is that the wrench end is
offset to the side (presumably to clear something), but the drive end
isn't offset to match. So the angle of the torque wrench
matters, just like with a crow's foot. Not the end of the world,
but this minor nuisance could have been eliminated by offseting the
drive end to match the wrench end.
Torqued all four nuts (in progressive increments) to the specified 96
in-lb, and gave them a dab of torque seal inspecion lacquer.
Aux battery
The auxiliary battery is 12 V AGM/VRLA sealed lead acid battery in the 2 to 3 Ah range.
I chose a common form factor, 7.00" long x 1.38" deep x 2.36" tall (excluding terminals), weighing approx 2 lb, with 0.187" faston terminals at opposite ends.
These are used in a variety of applications including uninterruptable power supplies for computer systems and medical devices. Form factor compatible products (capacity, temp ratings, and weight may vary some)
are produced by numerous manufacturers and are available through numerous distributors and retailers. Cost
is in the $15 to $30 range. Some manufacturers' p/n’s (an incomplete
list):
Panasonic LC-R122R2P (commonly used as the “generic” p/n on
cross-reference lists)
PowerSonic PS-1220 (better specs than Panasonic, my top choice)
EnerSys/Genesis NP2.3-12 (same company that makes the Odyssey line)
A Google search on LC-R122R2P yields many many more…
Note that the aux battery is quite small. During normal
operations, it is meant to power only an auxiliary EFIS and one P-Mag
during short periods of low-RPM operation where the output of the SD-8
may be insufficient. And it goes without saying, the little aux
battery is not used for engine starts. For "abnormal"
operations, a cross-feed mode (to be discussed in detail elsewhere)
allows the pilot to link the two electrical systems and maintain up to
full capability under a variety of fault conditions and combinations
thereof. Only under an extremely low-probability multi-system
failure where the main battery, main alternator, and aux alternator
are all unrecoverably off-line, is the aux battery the only remaining
power source for avionics and airframe functions, which would
constitute an emergency
Back to building... I'm mounting the battery on the forward side
of the starboard sub-panel. Fabricated a battery tray, and
provisions for two zip-ties to secure the battery to
the tray. Simple and effective.
Aux alternator support components
The various support components are mounted in the cockpit, on the aft
side of the starboard sub-panel. This location allows for easy
access for inspection/maintenance, and should keep the components
relatively cool. Before setting the component locations on the
sub-panel, I made sure to mark a keep clear area for where the canopy
frame comes down. Then it was just a game of tetris. And
the pieces fell right into place.
|

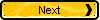
|
|